Diesel tricycles occupy an important position in urban and rural transportation due to their strong power, durability and reliability. As the core component of the vehicle, the maintenance of the diesel engine is directly related to the vehicle life and operational safety. According to statistics, failures caused by improper engine maintenance account for more than 65% of the total failure rate of diesel tricycles. This article will systematically explain the scientific maintenance methods of diesel engines from the three dimensions of fuel system, lubrication system and cooling system, combined with typical failure cases
- Refined management of fuel system
Diesel engines are extremely sensitive to fuel quality. Diesel with a water content of more than 0.05% will cause rust in the injectors. It is recommended to use automotive diesel that meets the GB 19147 standard and avoid using high-sulfur diesel (sulfur content > 350ppm) commonly used in agricultural machinery. The diesel filter should be replaced every 200 hours of work. Tests on a certain brand of TD25 engine show that the use of inferior filter elements will accelerate the wear rate of the injection pump plunger pair by 3 times.
The fuel tank maintenance needs to implement the “three-drain” system: drain the sedimentation cup after daily operation; open the drain valve at the bottom of the fuel tank for 10 seconds every week; add silica gel desiccant to the fuel tank breathing valve during the rainy season. For engines equipped with mechanical pumps, the oil pump should be manually pressed regularly to remove bubbles in the oil circuit. High-pressure common rail models should pay special attention to the fuel temperature. When the oil temperature exceeds 60°C, the heat dissipation device should be checked immediately.
- Periodic maintenance of the lubrication system
The engine oil selection needs to match the SAE viscosity grade and ambient temperature: 15W-40 is recommended for areas above -10°C, and 5W-30 synthetic engine oil should be used in severe cold areas. According to the tracking data of a certain agricultural tricycle, the overhaul cycle of an engine that changes the engine oil on time (every 250 hours) can be extended to 8,000 hours, which is 42% higher than the irregular replacement group. When changing the engine oil, the filter element needs to be replaced at the same time, and pay attention to cleaning the sealing surface of the filter element seat.
Oil pressure monitoring is an important early warning indicator: the oil pressure should be ≥0.15MPa at idle speed and ≥0.35MPa at rated speed. If abnormal pressure occurs, check the oil pump gear clearance (standard value 0.10-0.20mm) or crankshaft bearing wear immediately. Turbocharged engines should pay special attention to the sealing of the oil inlet pipe. Oil leakage will cause sintering of the turbine bearing.
- Scientific maintenance of the cooling system
Water-cooled engines need to regularly test the freezing point of the coolant, and the concentration of ethylene glycol should be maintained between 40% and 60%. The radiator needs to be backwashed with compressed air every quarter. Statistics from a maintenance station show that a radiator with more than 30% blockage will increase the water temperature by 12-15℃. The water pump belt tension needs to maintain a deflection of 10-15mm. Too tight will accelerate bearing wear
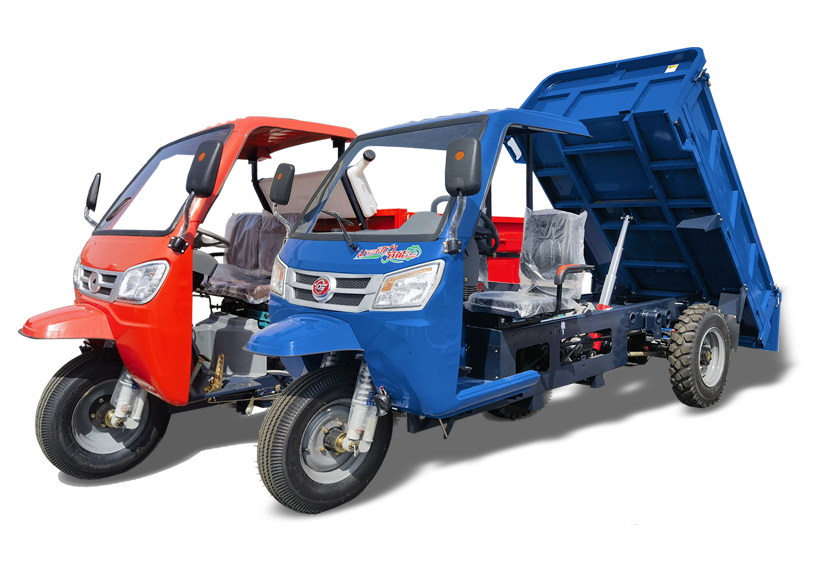
Cylinder liner cavitation is a common hidden fault. When the pH value of the coolant is lower than 7.5, it should be replaced immediately. For vehicles with frequent short-distance transportation, it is recommended to add anti-cavitation additives once a month. For air-cooled models, ensure that the deflector is intact. If the thickness of dust on the heat sink exceeds 2mm, the cylinder temperature will increase by more than 20%.
IV. Daily use specifications
Cold start operation directly affects the life of the engine: when the ambient temperature is below 5℃, the crankshaft should be idled for 5 turns first, and in winter, it needs to be preheated to the coolant temperature of 40℃ before starting. Avoid idling for a long time during work. An experiment has shown that the carbon deposits generated by idling for 30 minutes are equivalent to normal driving of 150 kilometers.
The load should be gradually reduced before shutdown. Turbocharged models need to idle for 3 minutes before turning off. Long-term parked vehicles should be treated with corrosion protection: inject 10ml of engine oil into the cylinder, seal the inlet and outlet with plastic wrap, and disconnect the negative electrode of the battery.
V. Regular inspection and maintenance
It is recommended to establish a “three-inspection” system: check the oil dipstick scale, coolant level, and belt status every day; check the battery voltage (should be ≥12.6V) and fan clutch sensitivity every week; check the carbon deposits in the cylinder with an endoscope every month. When starting difficulties, power drops by 10%, and oil consumption increases suddenly occur, professional diagnosis must be performed immediately.
Conclusion
Diesel engine maintenance is a systematic project that requires the combination of preventive maintenance and condition monitoring. It is recommended that users establish an “Engine Health File” to record each maintenance data. Transportation companies can introduce oil spectral analysis technology to predict wear trends by detecting the content of metal particles. Remember: a high-quality engine will save you 80% of the maintenance cost. Only by turning scientific maintenance into a daily habit can diesel tricycles truly become a reliable partner on the road to wealth.